Timber, what can I say…. well probably if you could be bothered listening you’d hear a lot of unintelligible colourful mutterings if you get me started and I’m having a bad day on the timber design……

Sometimes I’m a fan of timber as an engineering material, other times not. Some people create beautiful structures from timber, just not me.
I can see it is a comparatively ‘cheap’ material compared to steel or concrete, but from a design & detailing perspective it sometimes drives me to the brink of going nuts.
It’s relatively easy to design simple members, but also relatively hard to connect these for any ‘real forces’ or unusual configurations. It’s also easy for someone on site with a drill or saw to give you a bad day, usually, when they do something they have apparently ‘been doing for years!’ and try to ask for forgiveness after doing it.
You know the type of thing, that knob-end contractor saying during the last house they built that the designer let them cut out 80% of the depth of the joists and that they think you’ve over-designed everything anyway so it would probably be ok right? ……… This shit literally drives me nuts.
Yet there is pressure to use more timber from a sustainability perspective, I guess relative to other ‘engineering’ materials used in construction it can be viewed as being more sustainable. But if you must use two times the amount of timber to do the same thing today, than was actually ok a few years back due to code changes. Is that still considered sustainable?
And here we arrive at the point of this post (at least getting closer to the point). I’ve spent some time over the past few months looking through the impact of utilising the draft provisions in the recent New Zealand timber code revision, the NZS/AS1720.1 draft. Because it is coming…. [one day anyway]…
Timber or die..?
Sometimes I’d chose die, it’s just easier…. As a bit of a background for the more international people who chance upon this, in New Zealand we have a timber design code that is pushing 30 years old now. It’s been amended a few times primarily to continually reduce timber strengths to match the faster-growing but weaker timber we grow locally.
But otherwise, the engineering methods and theories behind the approaches in this standard have remained relatively constant for those years, being simply outpaced and left in the dust by continually evolving equivalent and arguably more advanced international standards like the European and/or North American standards. Those regions probably think their standards don’t get updated enough, but try waiting 30 years people, sit back down!
There have been rumours for like the last 20 years that the New Zealand timber standard required updating, and/or was going to be updated (ever since I was a young keen engineer, you know how we all were once upon a time!).
That time has apparently come with this draft version of the standard being issued a few years ago for comment, with an associated promise that it would be issued as final within a year or so. That timeframe has clearly passed and the goalposts have been once again shifted. But with nothing better to go on, I decided to have a look at the changes being presented in their current form.
This draft primarily piggybacks on the current Australian timber design standard AS1720.1, with some amendments for NZ use via an appendix. It was a bit of a dog’s breakfast way of doing things which I’m sure will be a real cluster to use in a practical design sense. Flipping between the two documents and changes to the symbols for almost everything is painful.
But some would argue it’s still a big step forward from dealing with the prior 30-year-old standard, which was not up to snuff for the way timber and especially mass timber is built and designed in the modern world. Apparently, a lot can change in timber knowledge in that time….
Anyway, here’s the point, for certain common things like a simple stud wall you could be using twice as much timber the day after this updated standard comes into use unless it is modified further which I’ll hopefully demonstrate.
Now I understand some progression in knowledge will mean some materials and methods get upgraded/degraded, that’s life. Those PhD types need something to do after all.
But some of the changes being proposed in the draft seem fairly heavy-handed and come somewhat out of the blue. I’ve personally never heard of there being any widespread or recognised issue with the axial capacity of timber for example. Why change something that has a history of working?
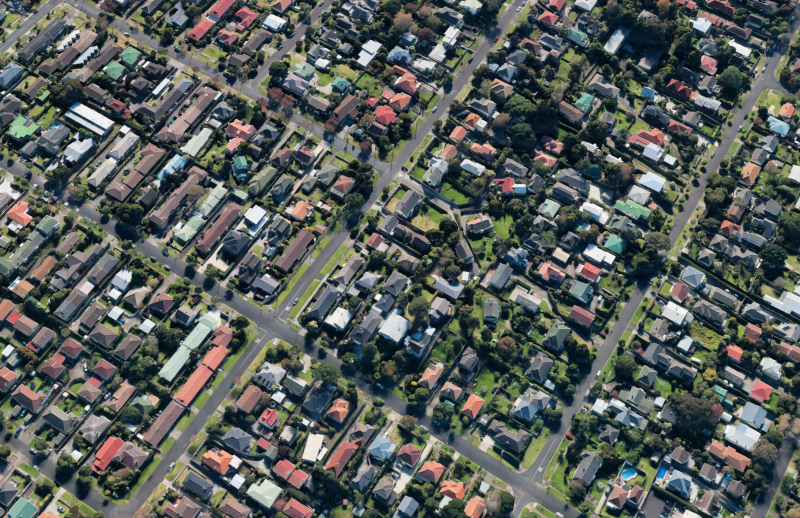
Sure, the current NZS3603 approach might be arguably less conservative than an equivalent international standard. But those buildings designed to NZS3603 and even NZS3604 are still standing right with no apparent issues…..
NZS3603 vs NZS/AS1720.1 approach to axial buckling…
In a nutshell, irrespective of the strength or stiffness of the timber, NZS3603 the current New Zealand timber standard has the same fundamental buckling curve based on the slenderness of a member. The only differentiator with this is whether the timber is considered as ‘Dry’ or ‘Green’ depending on moisture content. This buckling factor is termed .
Whereas AS1720.1 uses a formulation that counts on the strength and stiffness of the material to modify the buckling curve based on slenderness. This is achieved via the use of a material constant based on whether or not the member is ‘Seasoned’ or ‘Unseasoned’ timber. Essentially the same as the ‘Dry’ or ‘Green’ differentiator in bad old NZS3603. This bucking factor is termed .
In effect the axial capacity of a design to NZS3603 scales linearly based on material strength, whereas in a design to AS1720.1 you get some benefit from an increased strength but it’s not a matter of doubling the strength and getting double the capacity like it is in NZS3603.
Now it’s been a while since I did anything serious in Python, so we’ll use Python to compare the fundamental buckling curves and then the resultant capacities to show an example of what difference in capacity can occur for typical scenarios where for example studs might be 2400-3300mm long in a typical construction of residential houses (code linked at the end of the post):-
Comparing…
Let’s get into it, the following compares directly the capacity vs slenderness for NZS3603 and NZS/AS1720.1 draft standard. The comparison is shown for SG8 and various LVL grades with a standard 90×45 stud member: –
The first thing you’ll hopefully note is that all of the draft standard curves based on slenderness are well below the equivalent NZS3603 curves for the same timber grade. Red curves are below green curves! Bad news for designers, good news for those selling timber….
We can also plot the raw reduction in capacity for a given timber grade, by calculating the following ratio of capacities
So, hold onto your calculators… this shows for the typical stock standard SG8 stud at a slenderness of 25 you’re looking at about 65% of the NZS3603 capacity on a good day, and for LVL8 it gets all crapped on with about 40% of the NZS3603 derived capacity on a good day.
These reductions are fairly sizable and not a small adjustment or refinement, but they don’t tell the entire story and potential impact on design quite yet.
To elaborate, in NZ we have a non-Specific Engineering Design (non-SED) code NZS3604 which is typically used for sizing timber-framed buildings up to 2.5 storeys high. The half-storey is intended as attic space or for a foundation cavity, not habitable space for sheep or Hobbits.
Basically, it’s a whole lot of predefined tables and some guidance that they reckon architects can use even…. scared much!?
The basis of this code is rather unique, certain parts of the code seem to be based on some historical empirical approach, like ‘hey we’ve been doing this for years and it’s worked so far’, vs a sound engineering approach strictly based on the timber design standard of the day. Try out some numbers to some of the standard solutions and you’ll struggle to make sense of the recommendations as they just don’t work.
But as part of the ‘hey it worked so far’ approach, this standard actually utilises an effective length factor of 0.75 for working out capacities of studs under axial loading. Possibly a bit unrealistic, but ‘hey it’s worked so far’ right?
House image?
Compare this to the recommended approach in the recent draft, which suggests an effective length factor of 0.9 should be utilised for studs in light timber framing: –

So, to tell the full story in terms of how much the reduction in capacity might really be for a real-world design, we must factor the effective length factor into the formulation. If we plot the capacity vs actual stud length based on the 0.9 (for NZS3603 & NZS/AS1720.1) vs 0.75 (for NZS3604) effective length: –
Orange beats green beats red!
See it is possible for things to get worse, a valid design to NZS3604 using SG8 timber for your house suddenly loses ~55% of its capacity overnight as soon as you need to consider a Specific Engineering Design scenario to the prosed draft NZS/AS1720.1. Poor old LVL8 grade timber suffers the worst at ~30% of an NZS3604 based capacity.
Note the same is true of other typical framing sizes, 140×45 for example, but due to the better slenderness for out-of-plane buckling, the reduction isn’t as bad for typical framing lengths: –
Conclusion…
Now that sort of overall potential reduction in capacity sounds a bit crazy to me, something has gone off the rails. As I implied, houses are still standing irrespective of the design code. Maybe this reduction is the intent of the code writers. You’d just think they’d mention something that significant, and you know give a reason?
But possibly code writers don’t really design things in the real world and have no idea about the reduction because no one did any back-of-the-envelope calcs to see if adopting the Australian code directly was a good idea or not when compared to ancient code capacities.
I’m not aware of there being any prior discussion that the capacities were out by this sort of margin that might explain any of this.
However, the material constants for Australian use are just not suited/calibrated to NZ timber. But you’d think they would think of that right? After all these factors are based on the ratio of Modulus of elasticity to strength, which for Australian timbers are different to NZ timber after all.

Maybe you just got to go buy some shares in your local timber supply merchant and profit from the sale of twice as much timber (assuming you can even get some timber these days)…
Hey, I don’t write codes, I’d hate to oversimplify the process, I’m sure it is a challenge to satisfy everyone and everything especially when you’re updating a 30-year-old code with a lot of potentially out-of-date material….
But I’d like to think someone was looking at this to make sure things are not going off the rails and unnecessarily downgrading timber by a significant margin from what has been at one point in time a proven prior level of past performance.
Good luck on those timber builds, sounds like we’ll need it……
buy those shares in your local timber merchant and cross your fingers nobody changes the draft!
you heard it here first, sound investment advice
For the code visit the GitHub repository